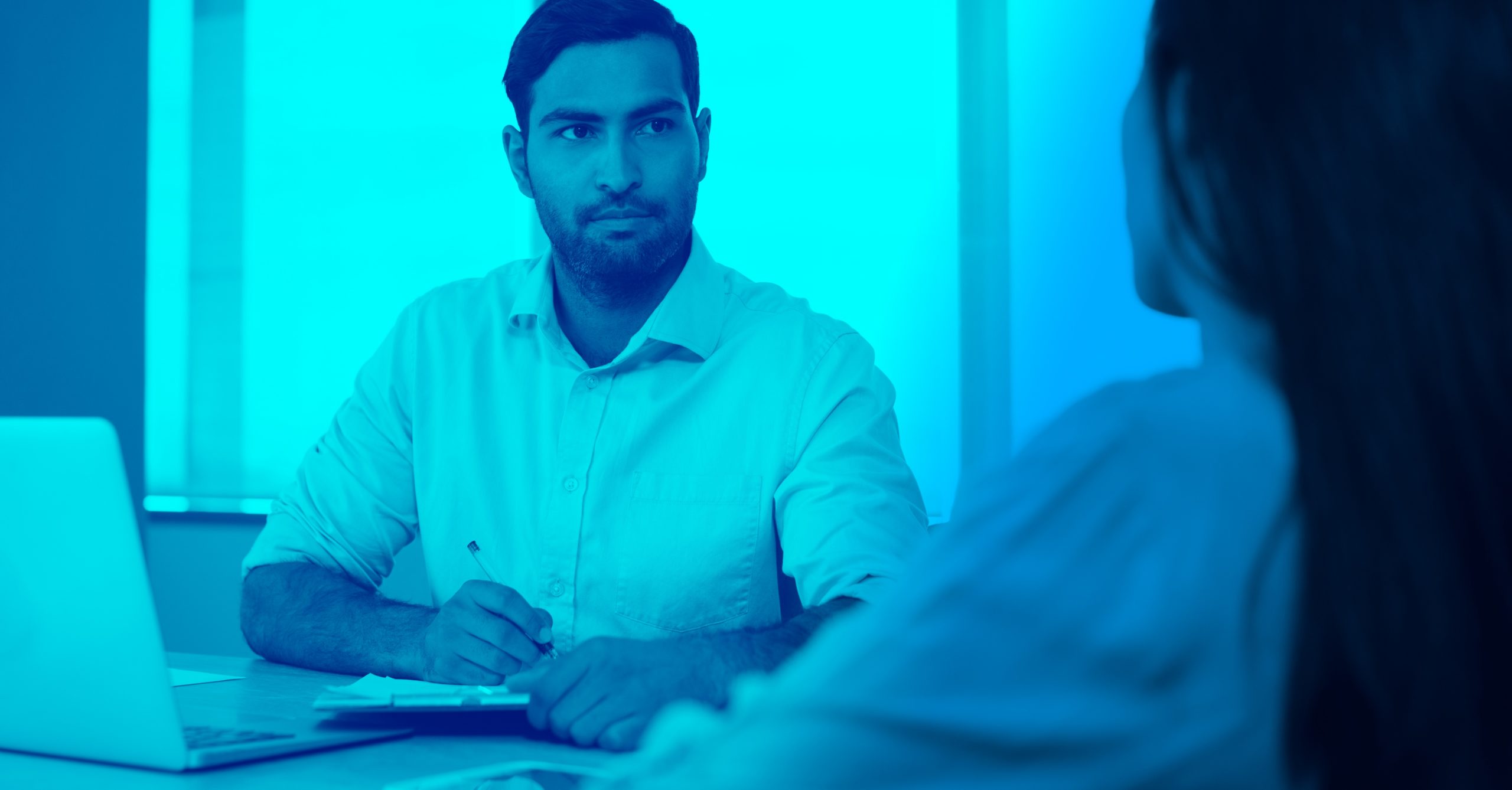
Why your Health System Needs a Contract Repository
May 17, 2022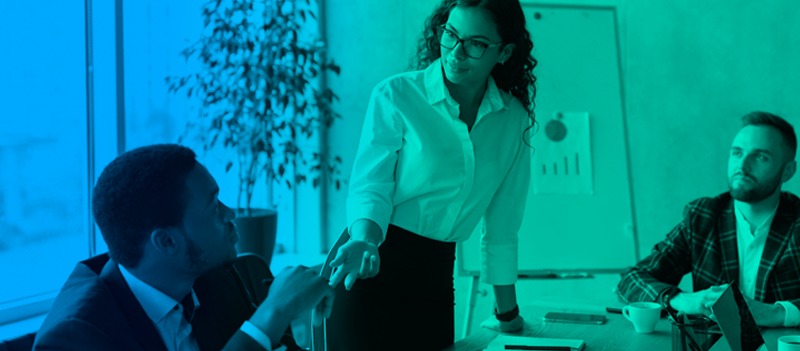
Why Health System P2P Leaders Need Spend Visibility (Spend Visibility Part 1)
July 26, 2022Managing contracts can quickly become burdensome with thousands of active suppliers being utilized in every health system. Organizations must create a centralized contract repository in order to manage their contracts and terms properly.
What is Process Mapping?
Process mapping, or process flow mapping, is the visual representation of how tasks are actually completed in a workflow. A process map brings visibility to who is involved in a process and sheds light on areas that need improvement. Thus, it is an excellent tool for establishing ideal processes and workflows. It can be as complex as mapping an entire organizational process or as simple as detailing an individual function within one position.
Process mapping provides awareness of a particular workflow. Comparing current process maps with an ideal map is known as gap analysis can be utilized to increase efficiencies. For example, health systems consistently struggle with recording returned goods creating a gap in the returned goods process. Without this record, the hospital does not complete a return and takes a loss on unused and outdated products.
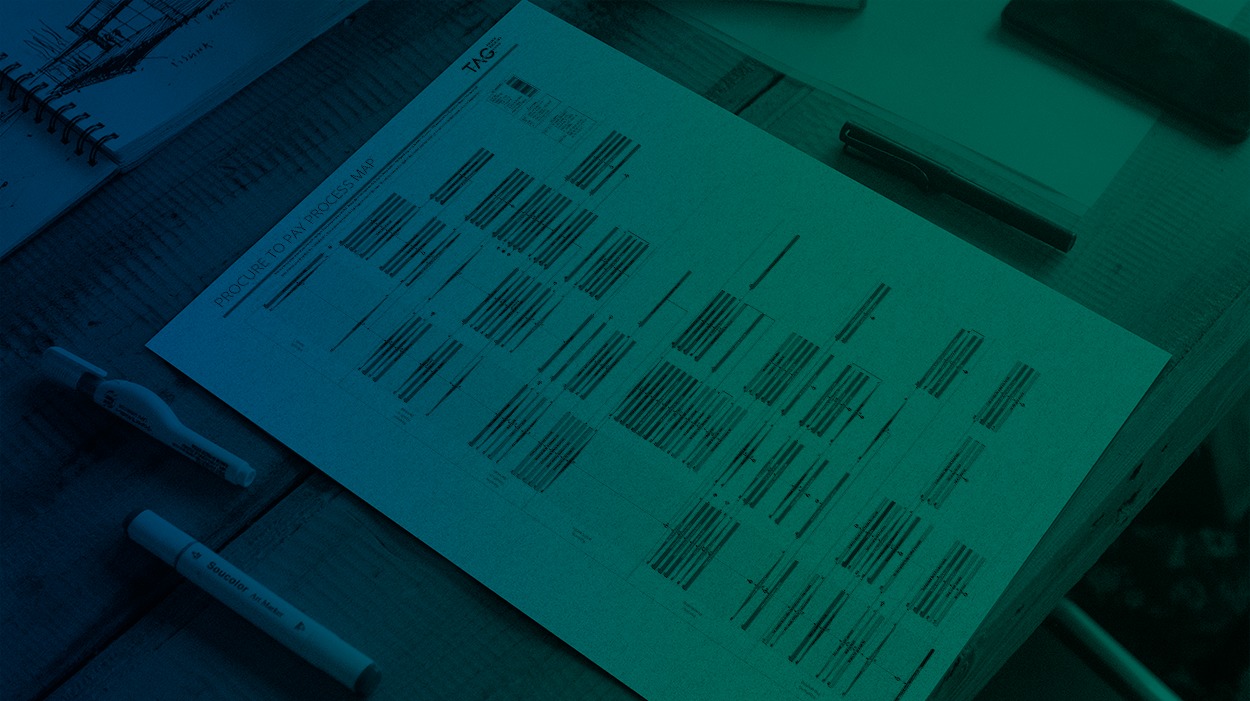
TAG combines contracting and spend data with health system’s current P2P process map to identify gaps and other anomalies. TAG then partners with the health system to close gaps to both stop financial leakage and gain efficiencies. Message us now to learn more.
Benefits of Mapping your Health System’s Procure to Pay Process
Process mapping is beneficial for any process across an organization. However, in this blog, we will focus on the P2P process in hospitals or health systems. Some benefits include:
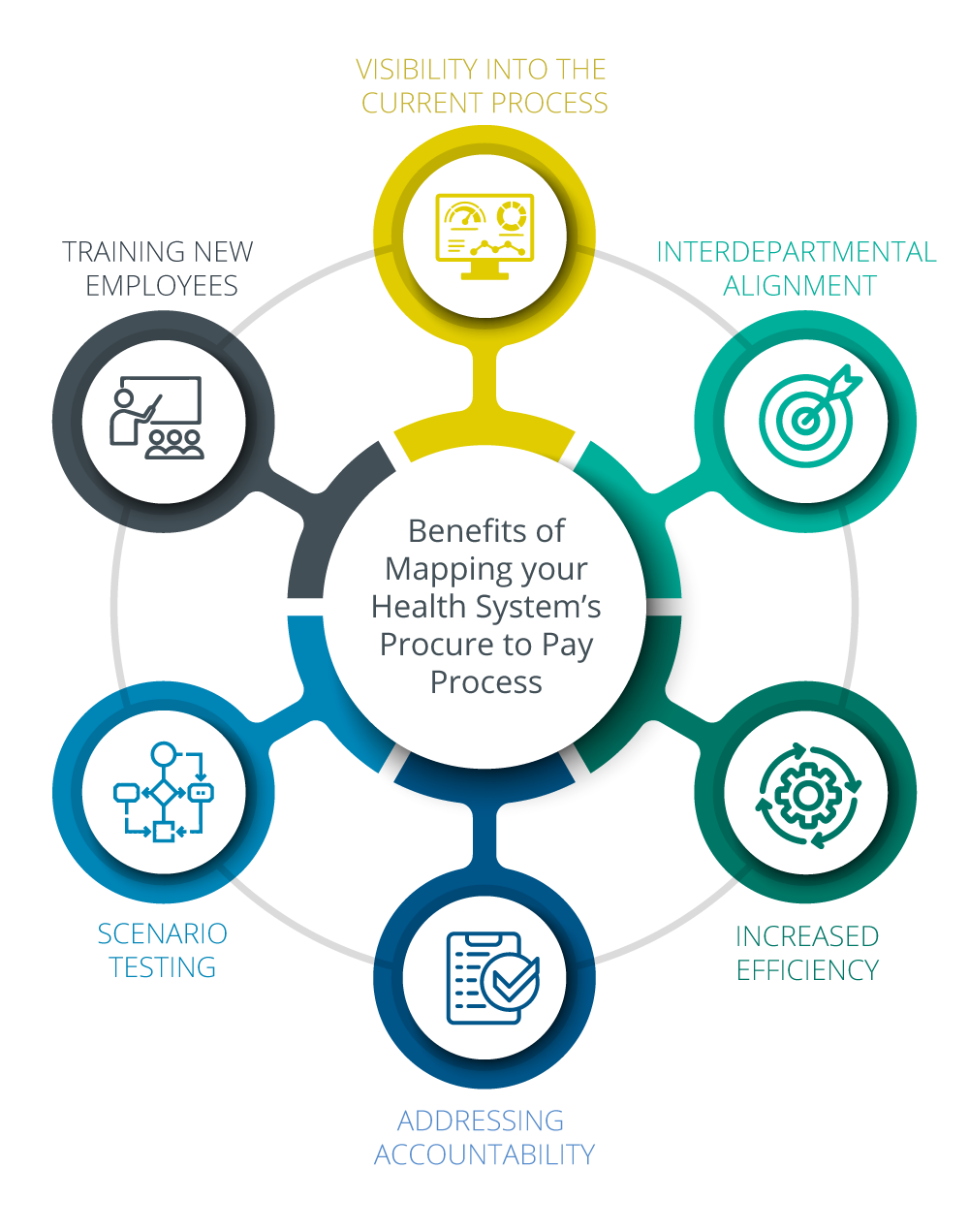
Visibility into the current process.
A P2P process map will visually show each step of the P2P process including who is involved and areas where rework and redundancies occur.
Interdepartmental alignment on the process.
Alignment of what each department does and who is responsible for each step will begin to break down siloes. This also increases the opportunity for interdepartmental collaboration – often an area of frustration between AP and Supply Chain.
Increasing efficiency.
Mapping out the process will uncover rework loops, which are opportunities for improvement. By minimizing the volume of work in a specific process tasks are streamlined and efficiency is gained. However, process maps can further improve efficiency in other ways such as eliminating redundancies, minimizing unnecessary accountability handoffs, and consolidating alternate paths in the process.
Addressing accountability.
Process maps should be created using a system that shows who or what department is accountable for each step. This is done by color coding each step. Not only does this ensure a particular department or person is assigned each step, but it also highlights anytime a process is handed off to another department. Handoffs are areas of risk where data, information, or responsibility can be dropped.
Testing scenarios.
When viewing a process map, it becomes much easier to test potential variations or what-ifs in the process.
Training new employees.
A process flow map is a great tool to use for training new employees. It can serve as a high-level trainer and as a great reference tool as the new employee becomes more comfortable with their role. Additionally, as a new team member moves beyond “doing” and starts asking “why”, it can help show their role in a bigger and provide meaning to their task.
How to Create a P2P Process Flow Map
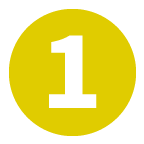
STEP 1: Identify the Process to Map
Deciding what process to map, including where that process starts (the first step) and where it ends (the last step), and in what amount of detail to map varies. The decision to create a process map usually stems from a problem or the need to understand and help various departments standardize some of their workflows.
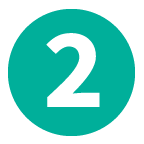
STEP 2: Determine the Sources You Need to Collect Process Information
Process data and information comes in numerous forms:
- Employees at all levels of the process doing the work
- Leadership and management
- Current process documentation
- Organizational policies
- Dark data sources such as email
- Third parties such as vendors/suppliers
With so many sources of information, it is essential to approach data collection in an organized way with the right team in place. Ideally, your process mapping team will consist of a facilitator, a person to collect and analyze the data, and someone knowledgeable about the entire process to take notes during interviews and observation.

STEP 3: Collect Data and Current Process Information
Begin collecting and organizing the data needed to map the process. This should include interviewing or shadowing staff at all levels of the process.
When collecting data consider these questions:
- Where does the process begin and end?
- What are the inputs and outputs of the process?
- Who and what departments perform tasks? When do these tasks?
- Are there redundant tasks?
- How often do variations in the process occur?
TAG TIP: When performing group interviews, it may be best to keep direct managers and leaders out of the meeting. Ensure the group understands that there are no wrong answers during the discussion. Also, help them understand that the document they are creating is a reflection of the actual events and actions that take place and that changes can be made along the creation process. If managers insist on being present, they must not question or “attack” team members that share deviations from any written process.
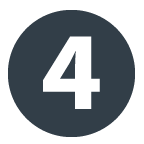
STEP 4: Organize the Steps and Tasks in Sequential Order
Begin mapping the order, focusing on the critical path first or the path that most often occurs. From there, fill in the variances that lie outside the critical path. Where possible, collect data around occurrences of each of the variances to boost the value of the map in determining whether a variance is an acceptable, rare occurrence or a more serious, frequent issue.
TAG TIP: Remember that this map will reflect the as-is process or current state. Comparing the current state map to an ideal process or standard operating procedures (SOP) showcases opportunities for improvement later.
Common Process Mapping Symbols
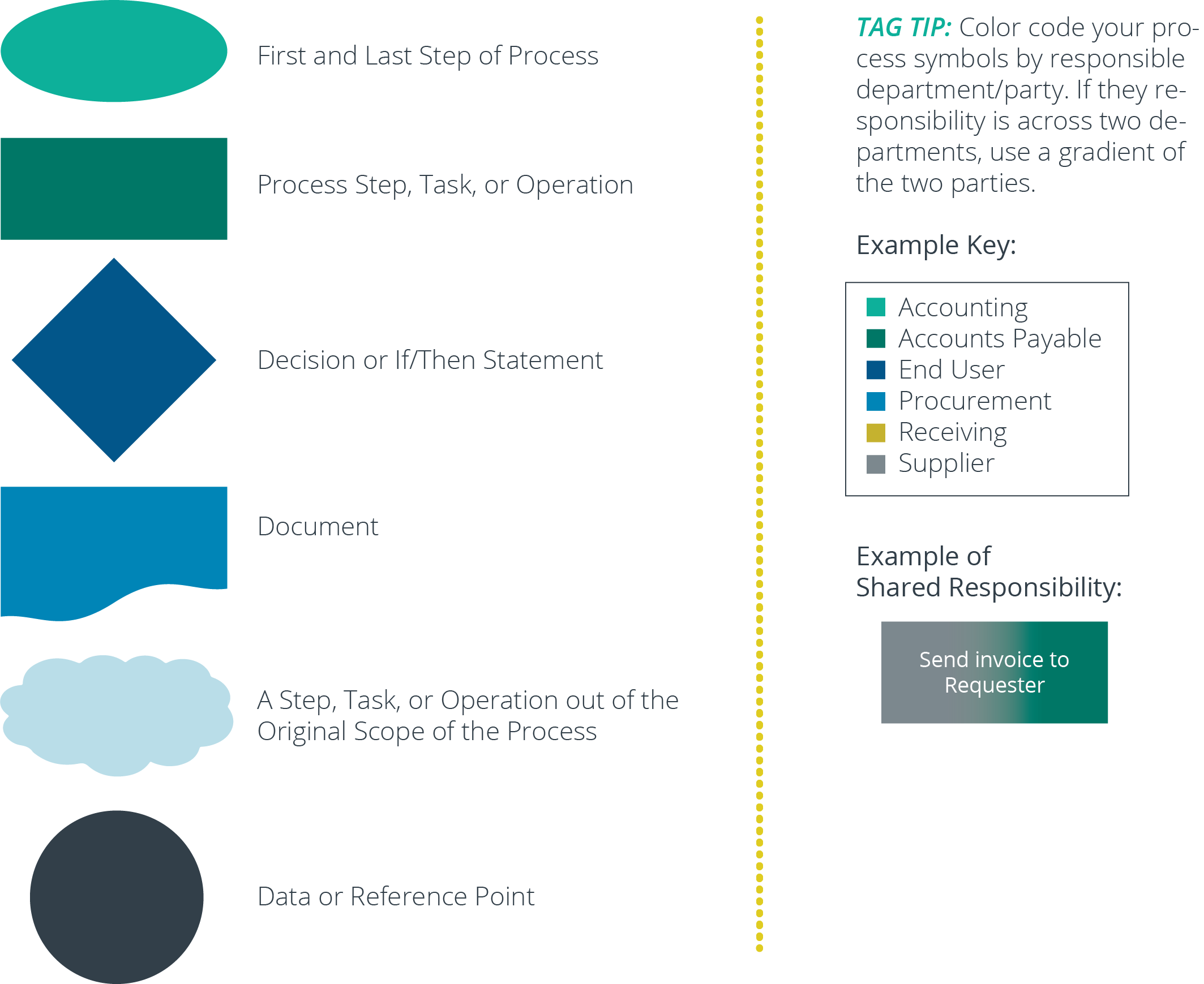
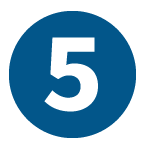
STEP 5: Review the Process Map for Accuracy
Review the map with those doing the work to ensure it correctly reflects the current process.
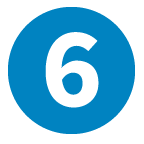
STEP 6: Analyze
Use these tools and methods to assess and identify process improvements with a current map in hand:
-
Ideal Process Mapping/Gap Analysis.
Creating an ideal process map will follow a similar process as mentioned above. When creating this map, it is also useful to include staff at all levels as they may have ideas for new controls or workflows that make their specific tasks more efficient. The team must then identify the areas of variances between the two maps that indicate process gaps.
-
Process Detail Report (PDR).
TAG’s proprietary tool for adding value to health system’s P2P process map provides a different look at the various steps or tasks in a process. This report documents:
- The inputs and outputs of every step of the process
- All tools used to complete each step
- Any metrics or KPIs tracked during every step
- Both the accountable parties and responsible parties at each step.
-
Transactional Data Analysis.
Combine all transactional and error data with your current process map showing how many of these errors occurred at each step. For example:
- How often do invoices become exceptions and require rework
- How many returns go through a certain process
- How many payments go through each pay type/method
- How many POs are processed electronically vs. manually
- How many invoices are processed with EDI vs. manually
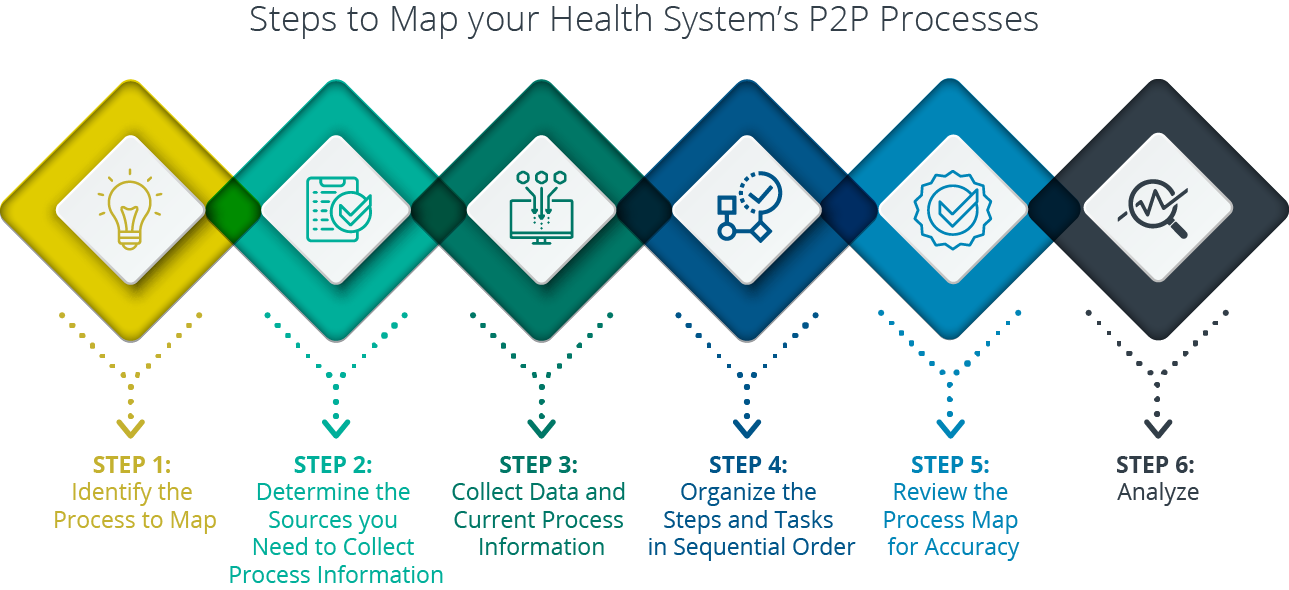
Challenges when Creating a Process Flow Map
While collecting and organizing data in itself is challenging, there are several impediments to be aware of along the way. This includes:
- Team members are reluctant to document parts of the process performed outside of their expectations out of fear of having to defend it.
- Team members feel that rework is inevitable and inconsequential and may be hesitant to mention such steps.
- Lack of metrics around certain activities or actions potentially hiding root issues.
- Rework may occur during the mapping process and new information appears while building the map.
How to counter these challenges:
- Ensure everyone involved understands the importance of making the flow chart accurate and complete.
- Make sure team members understand there are no consequences for telling the truth.
- Shadow team members and observe the process in real life.
- Allow sufficient time to work with all involved to document all relevant steps.
Process mapping is not an easy or quick project and may suck resources. Hiring non-bias parties such as TAG will take the least amount of resources to create a process map.
TAG specializes in P2P processes and performs process flow mapping for health systems and hospitals. A process map combined with a Discovery Review provides insight into health systems’ dark data and process gaps. Contact TAG and begin mapping and improving processes today.
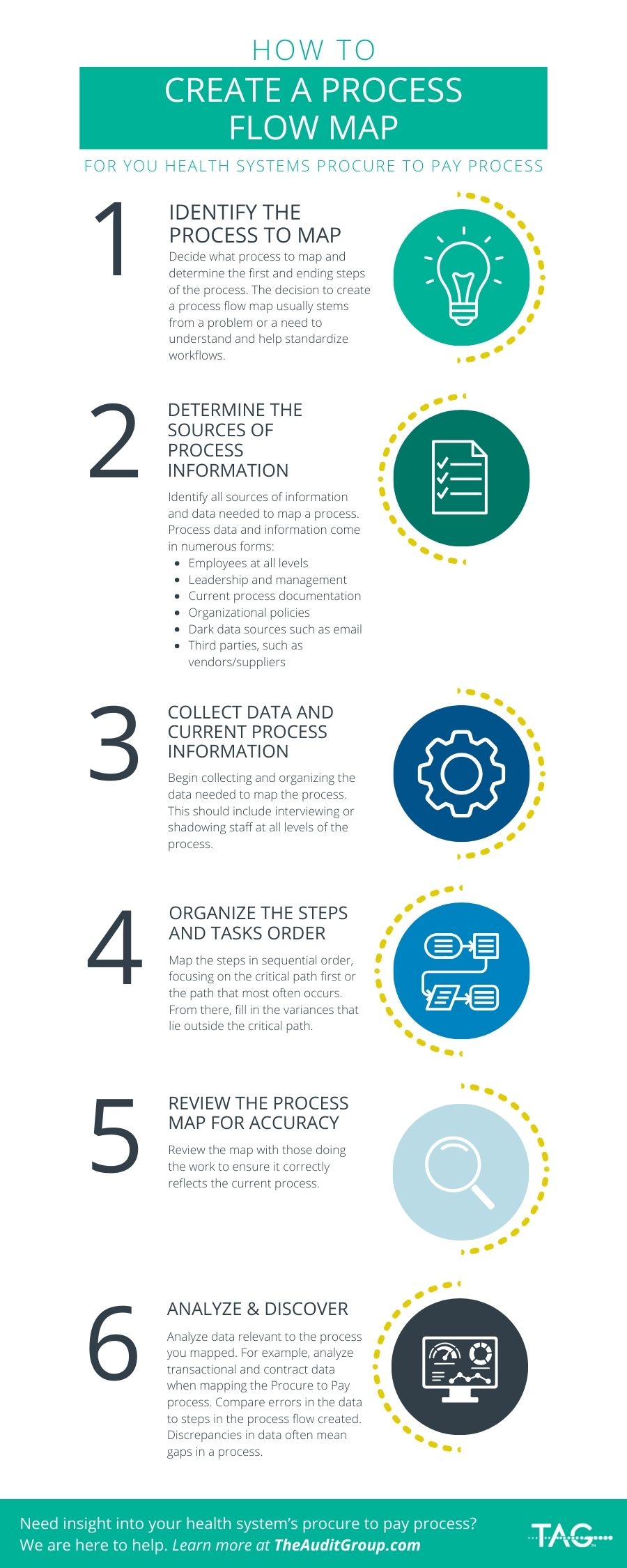