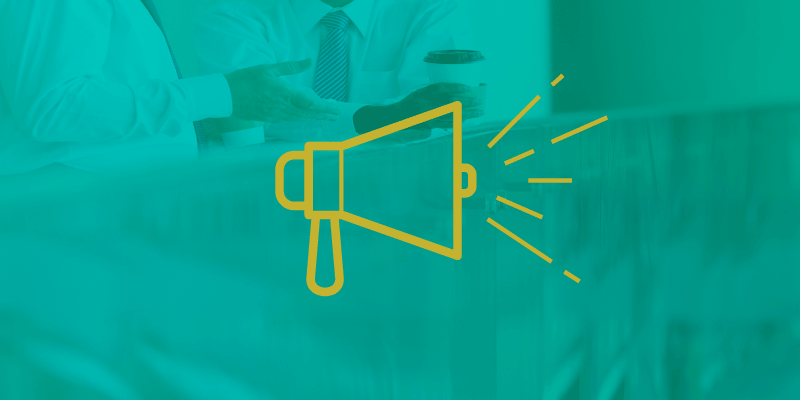
Press Release: TAG, Inc. Saved Healthcare Systems $4M first month of Pay-It-Forward Recovery Program
June 4, 2020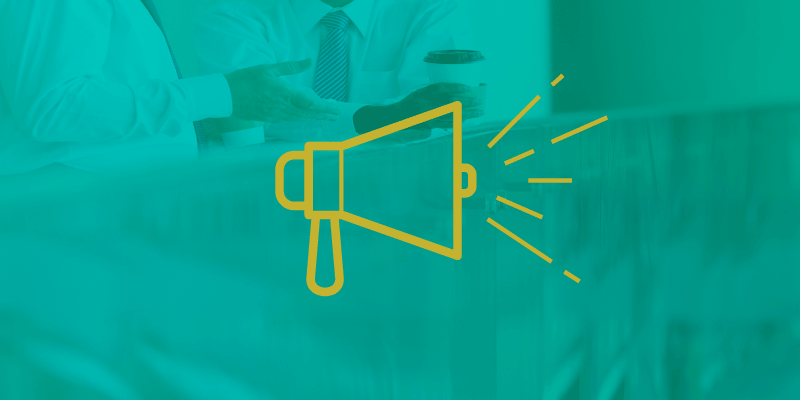
TAG, Inc. Saved Healthcare Systems $6M+ in Two Month Pay-It-Forward Recovery Program
July 1, 2020Healthcare systems return an average of 4% of the products they purchase each year. Of that amount, 7% of the amount returned never gets credited back by the vendors totaling a loss of $700,000,000 annually.*
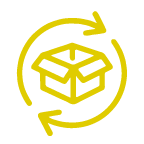
in returned goods credits lost each year
Why does the Returned Goods Process Lose Millions?
The returned goods process is an incredibly important area, spanning multiple departments of every health system. In theory, it is a relatively simple concept – return unused products and get your money back. However, the repercussions of mismanaging the process are significant. Organizations that mismanage their returned goods processes face a lengthy and challenging reconciliation process but more importantly lose valuable capital and time at an exponential level that could be spent trying to improve the quality of care.
Consider returning goods as an individual. You want to buy a pair of shoes but you are unsure what size you wear in this particular brand. You go to the website where the price is listed clearly and choose your normal size and one larger or smaller to ensure you get one that fits. You try both on, pick the option that best suits you, and return the other back to the supplier. The freight is often prepaid on the return, and you receive a confirmation email when the credit is posted back to your card. You check for the refund and you see that everything is in order. You used ONE vendor, ONE transaction, ONE carrier for your returned product, and you monitored ONE refund/credit. In all, it is a fairly simple interaction that you likely complete several times a year.
Now consider a healthcare system buying $150,000,000 worth of product over a year from as many as 1,000 vendors and returning thousands of items totaling more than $5,000,000 in value. Prices vary wildly, contract terms fluctuate and some items on purchase orders and some are not. The follow-up and monitoring process alone is significantly more challenging and there are no return confirmation emails.
There are significantly more factors at play including:
- A multitude of return carriers
- Tracking numbers
- Sources of the return
- Varying levels of information captured
- Differing dollar amounts expected back
Instead of having your card credited with money, you have a credit memo posted to an account statement for future use.
Most importantly, the increased complexity is only part of the story. There is a much greater financial risk than with a single pair of shoes!
With a large number of variables, it is incredibly important that organizations take control of their returned goods processes and ensure that they are as efficient and thorough as possible. This is no small task and this blog would be more of a novel if it were to describe all of the steps necessary to achieve an optimized returned goods process. No two health systems are alike, but all high performing returned goods processes seek to understand the dynamics of the departments involved, provide a safety net to the organization, and contain key elements that promote success.
Establishing a Process
Establishing a comprehensive and system-wide process should capture buy-in from the following departments:
- All Finance and Supply Chain Management
- Accounts Payable
- Purchasing/Materials Management
- Shipping and Receiving
- End Users
Providers should form a committee with members from all of these departments when creating a new returned goods process. This will ensure there is a platform for all involved parties to voice concerns, ask questions, and provide feedback. Process changes are more easily adopted at the system level when all parties understand how their responsibilities affect the group.
An optimized returned goods process provides health systems with the following:
- The ability to reconcile your returns with your vendors
- Vendor and departmental accountability
- Maximized value of the outstanding return dollars
- Departmental budgetary accuracy
- Accurate end of year accruals
Bolstering the returned goods process allows an organization to flip the power dynamic that is so commonly controlled by the vendors in the industry. By maintaining an accurate and detailed log/module providers gain the ability to make the vendors own their oversights and maximize the value they are entitled to. Each department’s budgets are impacted positively when the expected funds are returned timely and appropriately.
The Ideal Returned Goods Process
The ideal returned goods process contains the following elements:
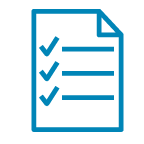
Tracking module/log that captures the appropriate information
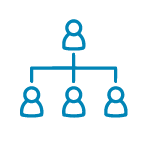
Defined roles across the health system
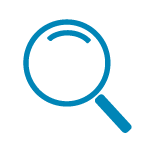
Process oversight and ownership
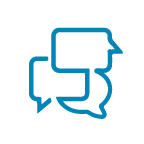
Strong and frequent interdepartmental communication
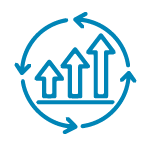
Continual improvement
As stated, returning goods is a simple concept but should not be taken lightly. Creating a defined and optimized returns process is an essential step towards protecting your healthcare system. A process that contains the elements listed above and the buy-in from the appropriate stakeholders will create a safety net that you can depend on.
Building in the practice of internal review allows for proactive improvement and growth rather than a reactive and retroactive approach so commonly observed in this industry.
Lacking the resources to design, test, and launch a new returned goods process? Let us help! We offer a returned goods optimization service that maps our client’s current processes, determines the gaps where funds are leaked, and designs a customized solution around industry benchmarks to put an end to lost credits and increases your organizational efficiencies.
*Averages and estimates provided were calculated using trends discovered at our clients’ health systems.